Hoppers
Hoppers are used for the elevation and parts feeding and handling of products. This type of system provides solutions to ergonomic problems (loading height), optimizes the flow in dispensers, or directly supplies material to machines (multi-head weighers, metering machines, etc.).
Hoppers can be designed for a variety of applications and adapt easily to plastics, food-processing, car, and cosmetic production lines. They are particularly well-suited for difficult environments, such as those with high temperatures.
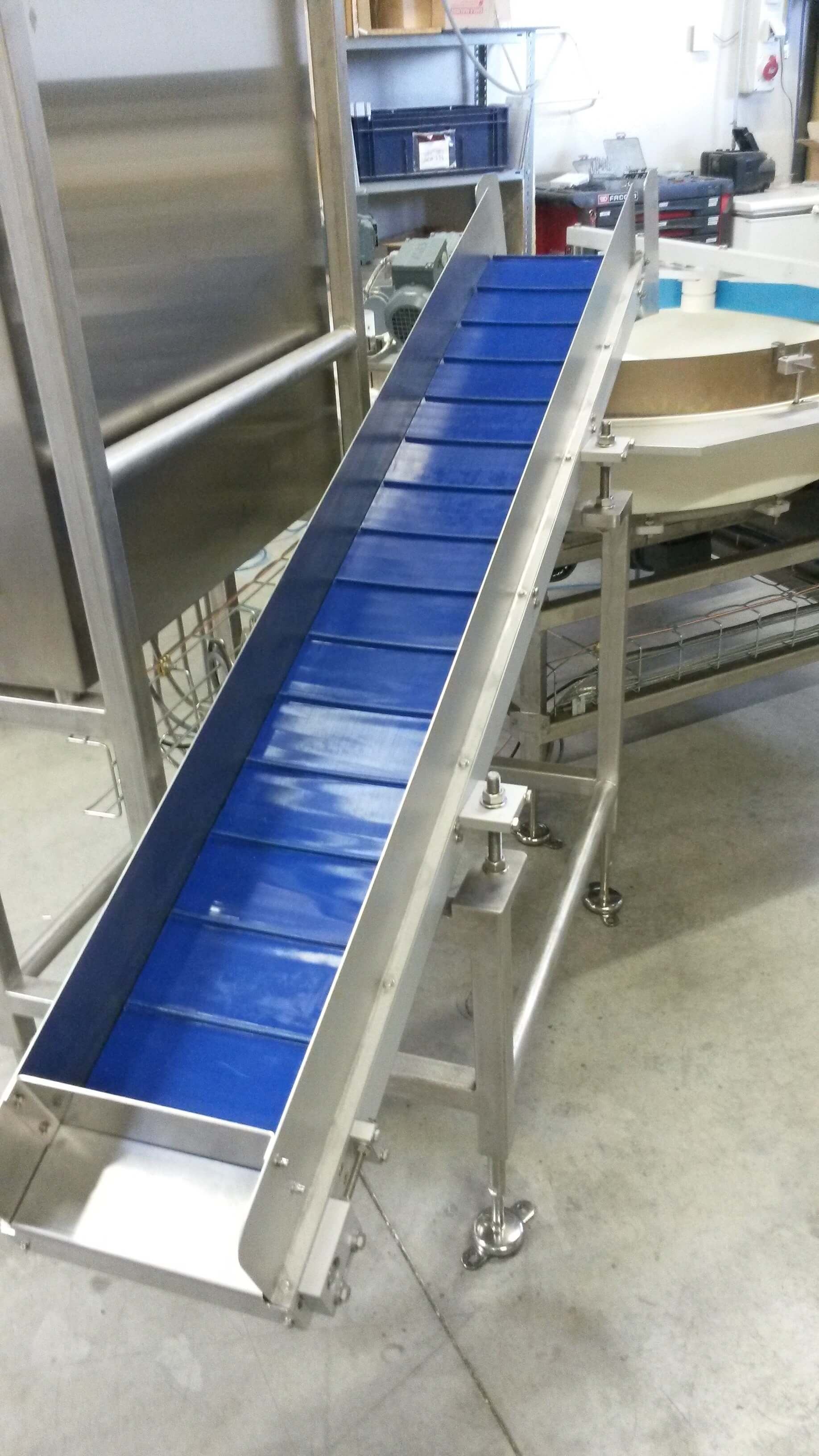
1- Hopper conveyor
Hopper conveyors are available in several versions:
– inclined belt
– lifting hopper with profiled belt
– vibratory hopper paired with elevator
– double-belt hopper conveyor for large storage volumes or heavy loads
– hopper bucket conveyor
Practical information:
– as an option, soundproofing and/or dust covering
– sizes according to specifications (volume, height, etc.)
– complies with FDA food regulations and EU standards
– storage bin made of stainless steel
– discharge chute made of stainless steel and adapted as needed
– protective cover against dust
– hopper bin level detection
– control and management panel for feeder flow
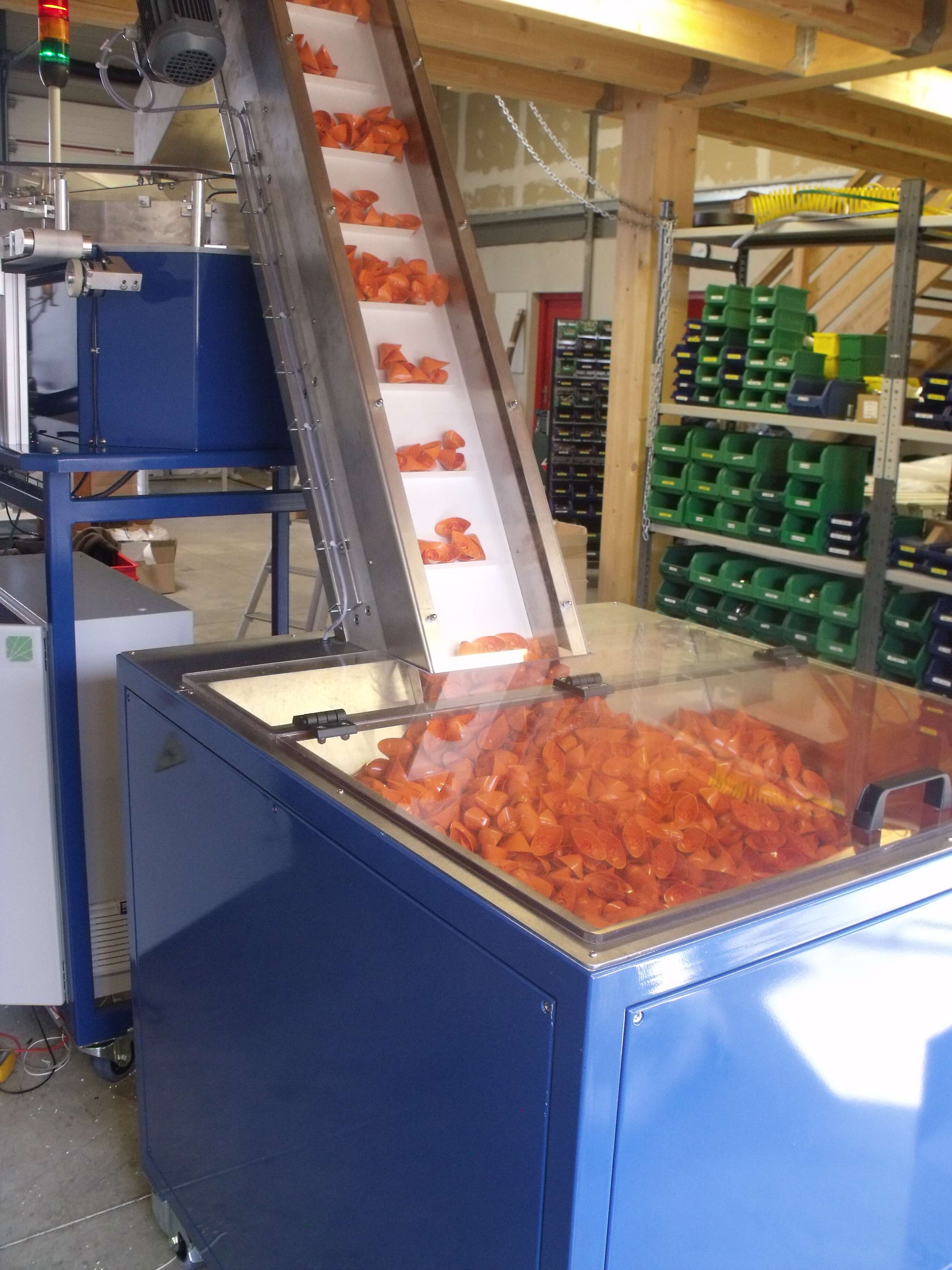
2- Orienting hopper
The orienting hopper dispenses or directs cylindrical parts that have a length greater than the diameter, such as shafts, pins, corks, etc.
Variation:
– lifting and orienting hooper for caps
Advantage:
– high feed rate
Practical information:
– hopper conveyor designed to suit the shapes of the products to dispense